PRODUCTS CENTER —— 产品展示 —— |
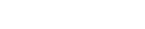
24-hour hotline
18002573585 |
|
|
Displacement Sensor Used in Tool Damage Detection of Machine Tools
With the rapid development of industrial automation, the automation degree and production efficiency of CNC machine tools have also been greatly improved. With a small amount of machine tools, production failures can be quickly found through manual inspection. For FMS, CIMS, unattended factories, etc., it is necessary to solve the problem of on-line real-time monitoring and control of tool damage. If the tool of the machine tool is worn or broken, the unprocessed or incompletely processed workpiece will flow into the next working procedure, which may cause secondary damage to the following equipment. Seriously affect product quality, production efficiency, maintenance cost and maintenance cycle.
At present, there are many schemes for detecting tool damage in the industry, but the direct measurement method based on linear displacement sensor and LVDT displacement sensor, and the indirect measurement method based on laser displacement sensor, ultrasonic displacement sensor and correlation sensor are the mainstream. The linear displacement sensor and LVDT displacement sensor are fixed at a certain position in the machining area of the machine tool because of contact measurement. During machining operation, the tool first moves quickly to the front of the sensor, and then decelerates to move forward for a short time. If the sensor sends a signal, and the signal is within the preset value range of the system, then the tool is normal. If the signal collected by the sensor deviates from the preset value, it means that the tool is broken or badly worn, and the equipment will stop working and wait for maintenance.
Laser displacement sensor, ultrasonic displacement sensor and correlation sensor are non-contact, so the tool can move quickly to the detection area of the sensor during machining operation. If the sensor feedback signal is within the normal range, the tool is normal. If the feedback signal is abnormal, the tool is broken or badly worn. Non-contact measurement method has higher working efficiency because it does not need deceleration operation. However, light, electricity, water, oil, dust and other factors in industrial field are complex, and the performance of non-contact displacement sensor is seriously limited. Taking photoelectric displacement sensor as an example, if it is affected by cooling liquid and oil mist of mechanical equipment, the measurement accuracy and reliability of the sensor will be greatly reduced, which will easily lead to false alarm or functional failure. If the sensor is installed far away from the processing area, this kind of fault can be effectively avoided, but it will increase the design difficulty and reduce the working efficiency.
Considering comprehensively, the direct measurement method based on linear displacement sensor and LVDT displacement sensor has higher stability and applicability, and is widely used in automation field. Rapid determination of tool damage degree and real-time on-line control are not only the basis of ensuring production efficiency and product quality, but also the key factor of prolonging equipment life and reducing equipment maintenance cost.
|